현대·기아차의 경량화 기술 추진 전략-현대차자료펌
현대·기아차의 경량화 기술 추진 전략
2019-12-24
가벼운 것이 곧 기술력인 시대다. 가볍고 더 단단한 소재를 개발하고 적용하는 것은 자동차회사의 선택이 아니라 생존이 걸린 필수 조건이 됐다. 현대·기아차의 경량화 기술 추진 전략에 어떤 것이 있는지 알아봤다.
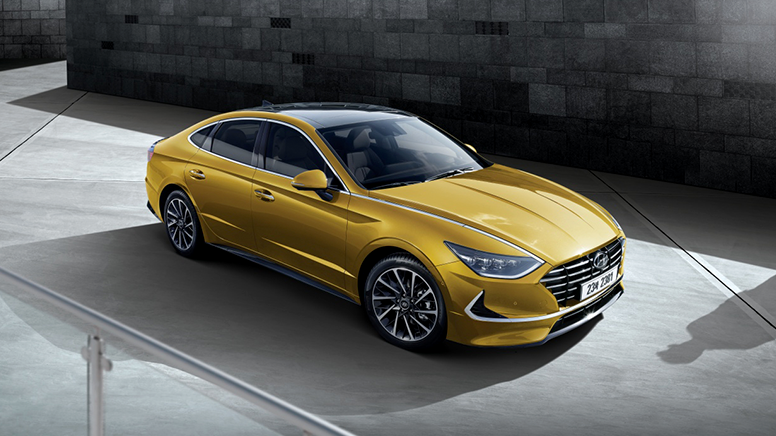
언제부터인가 자동차를 논하는 데 있어 ‘경량화’라는 말이 빠지지 않고 등장하고 있다. 살을 빼기 위한 수많은 다이어트 비법이 넘쳐나듯이, 조금이라도 더 가벼운 차를 만들기 위해 모든 제조사가 각자의 기술과 역량을 모으는 중이다. 경량화는 자동차의 연료소비효율(연비)과 친환경성 뿐만 아니라 운동성능을 향상시키는 핵심 기술이기 때문이다.
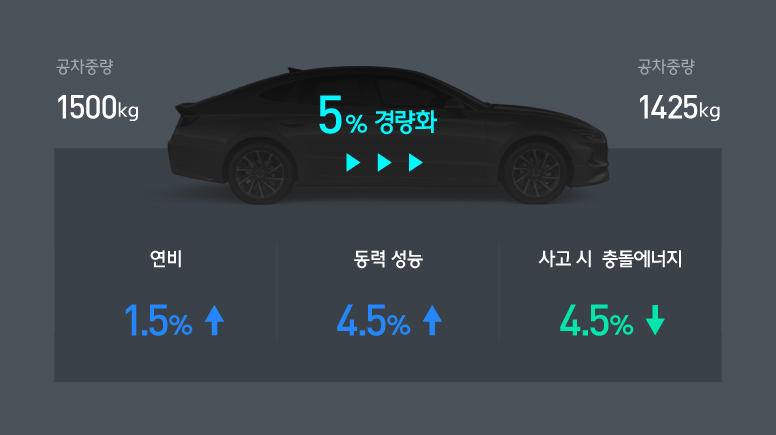
실제 공차중량 1,500kg인 중형 세단의 무게를 5%(75kg) 줄이면 연비는 1.5%, 동력 성능은 4.5% 향상되며, 가벼워진 차체가 충돌에너지를 약 4.5% 낮춰줌으로써 사고 시 차체 변형과 승객 상해까지 줄일 수 있다. 동시에 움직임도 날렵해지기 때문에 가속도 향상, 경쾌한 코너링, 제동거리 단축 등으로 이어진다.
환경적인 측면에서 배출가스도 줄어든다. 차가 가벼워진 만큼 엔진의 부하가 적게 걸리기 때문이다. 2020년부터 북미, 유럽 등 세계 각국의 배출가스 규제가 훨씬 강화되는 탓에 경량화는 더 이상 선택의 문제가 아닌 필수가 된 지 오래다.
자동차에 불고 있는 전동화 및 안전, 편의사양의 증가도 경량화를 해야 하는 이유 중 하나다. 하이브리드 자동차는 기존 엔진에 배터리와 전기모터가 추가되므로 당연히 무게가 늘 수밖에 없다. ADAS(첨단 운전자 보조 시스템)와 헤드업디스플레이, 파노라마선루프, 쿨링시트 등 안전, 편의사양의 증가로 차의 기본 무게도 점점 늘어나고 있다.
비용을 생각하지 않고 무게 자체를 줄이는 데에만 목적을 둔다면 얼마든지 단기간 내에 그 목적을 달성할 수 있다. 무작정 가벼운 소재를 사용해 차를 만들면 그만이기 때문이다. 그러나 현실적으로 쉽지 않다. 가벼우면서 강한 소재는 모두가 알고 있듯이 가격이 굉장히 비싸다. 특히, CFRP(탄소섬유강화플라스틱)는 기존 철강 대비 무게를 절반 정도로 줄일 수 있지만 가격은 무려 10배 이상 비싸다.
포르쉐가 이 CFRP로 휠을 만들어 기존 합금 재질 휠 대비 8.5kg을 줄이는 데 성공했지만 휠 가격만 2,000만원에 육박한다. 이러한 특징 때문에 일반적인 적용이 쉽지 않은 게 현실이다. 알루미늄도 무게를 20~30% 줄일 수 있는 좋은 소재지만 역시 가격은 2배 이상 올라간다.
이처럼 쉽게 쓸 수 있는 경량 소재는 결국 차량 가격 상승으로 이어지기 때문에 강성과 안정성, 그리고 경제성을 모두 확보하면서도 중량을 줄일 수 있는 기술 개발이 사실상 더 어렵다. 현대·기아차는 수년 전부터 플랫폼, 섀시, 파워트레인 등 자동차의 전체 시스템에 대해 경량화 기술을 개발 중이며, 현재 몇몇 차종에서 그 결실을 보여주고 있다. 물론 충돌안전성도 더욱 올라갔다.
경량화와 튼튼함은 반비례 관계지만 기술로 극복 가능
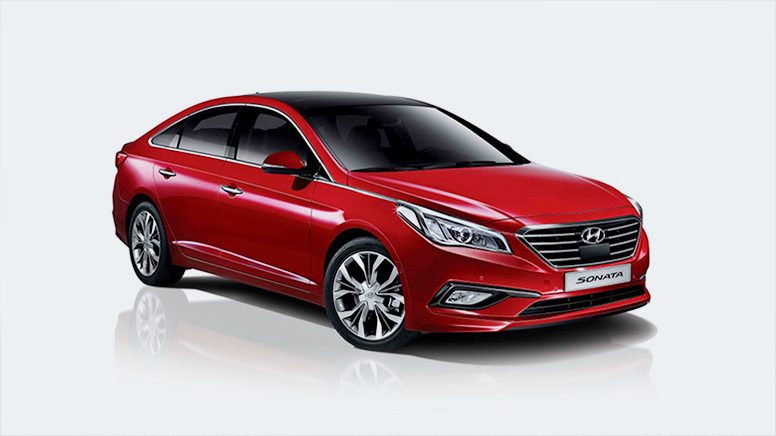
과거 현대·기아차는 차의 성능과 안전에 먼저 집중했다. 2014년 나온 현대자동차 7세대 ‘LF 쏘나타’는 6세대 YF보다 몸무게가 45kg 늘었다. 대신 각종 충돌 테스트에서 좋은 성적을 받으며 차체가 약하다는 이미지를 크게 개선했고, 고속주행 안정성과 핸들링도 크게 좋아졌다. 소음·진동(NVH)도 함께 개선됐다. 실제로 7세대 쏘나타는 출시 당시 “잘 달리고, 잘 돌고, 잘 선다”는 평가를 받았고, 주행성능에서 이전 모델과 비교해 획기적인 성장을 이뤘다는 평가가 많았다.
우선적으로 차체 강성을 확보한 현대·기아차는 다음 단계로 안정성을 더욱 높이면서 무게를 줄이는 전략을 실행했다. 가급적 값비싼 소재 사용을 자제하면서 경량화와 가격, 두 마리 토끼를 동시에 잡는다는 목표를 세웠기 때문에 이를 구현해내는 기술 확보가 만만치 않았다.
가벼우면서 강한 차, 신형 쏘나타의 경량화 비법은 구조 최적화
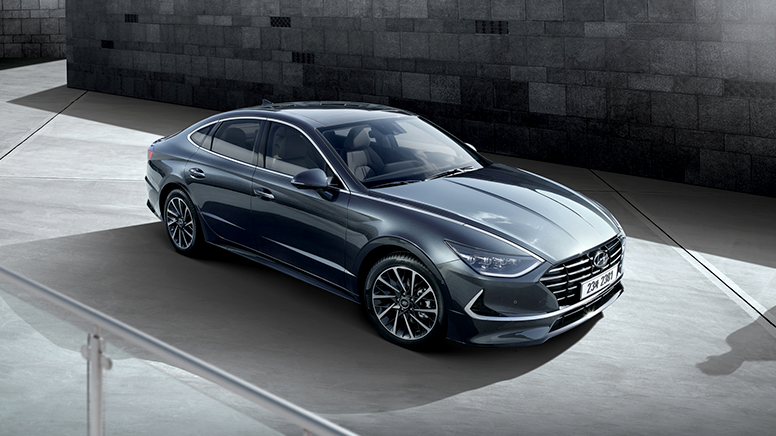
현대·기아차의 경량화 기술 성과를 확인할 수 있는 차가 바로 올해 3월 출시된 8세대 쏘나타다. 이번 쏘나타는 스마트 디바이스라는 콘셉트에 걸맞게 각종 첨단 기술이 탑재되면서 전자장비의 무게가 증가했다. 그러나 전체 무게는 낮추고, 전 세대 대비 충돌안전성은 높인다는 목표로 개발됐다.
이 때문에 연구소의 모든 부서는 비상이 걸렸다. 나사 하나와 전선 한 가닥의 무게까지 신경을 써야했기 때문이다. 설계 단계부터 플랫폼, 내·외장, 섀시, 전자장비 등 전 시스템에 경량화 기술을 적용해 최종적으로 전 세대 대비 약 59kg의 무게를 덜어낼 수 있었다(북미사양 기준, 국내사양 기준은 전 세대 대비 65kg 중량 감소). 안전, 편의사양 증가 등 상품성 개선을 위해 늘어난 부품 무게 27kg을 감안하면 사실상 총 86kg을 줄인 셈이다(국내는 92kg 중량 감소).
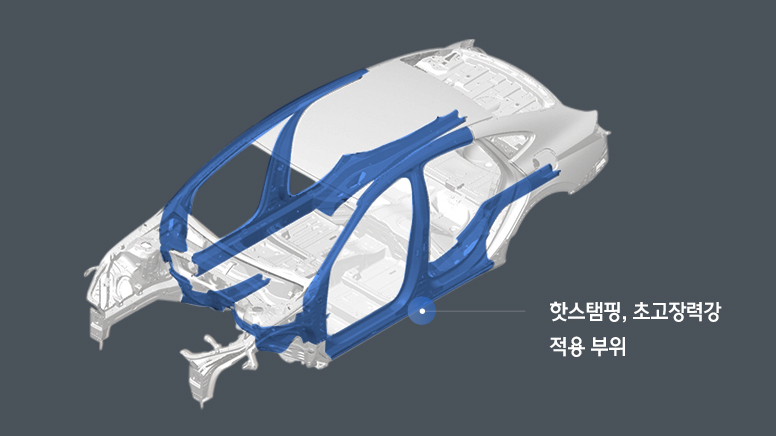
신형 쏘나타는 설계 단계에서부터 강성과 경량화, 두 가지를 목표로 구조 최적화 작업이 진행됐다. 초고장력 강판을 부위마다 두께를 다르게 성형하는 TRB/TWB(Tailor Rolled Blanking/Tailor Welded Blanking) 공법을 통해 차체 언더바디 강성부재를 최적화했고, 핫스탬핑 적용부품을 기존 16개에서 21개로 확대 적용했다. 또 바디 제어기의 기능을 통합해 부품 수도 줄였다.

그 결과, 신형 쏘나타는 북미 기준으로 1,415kg이라는 가벼운 무게를 달성했다. 글로벌 경쟁 모델 대부분이 1,400kg대 중후반인 것과 비교된다. 북미에서 동급으로 평가받는 도요타 캠리, 혼다 어코드와 비교해도 경량화 우위에 있음을 확인했다. 중량 뿐 아닌 충돌안전성도 동시에 높인 것은 물론이다.
동일 모델을 국내 기준으로 비교하면 차이는 더욱 뚜렷하다. 엔진 배기량 등 사양에 다소 차이는 있지만 신형 쏘나타(스마트스트림 2.0ℓ) 1,405kg, 도요타 캠리(2.5ℓ) 1,580kg, 혼다 어코드(2.0ℓ 터보) 1,550kg으로 중량 차이는 더욱 명확히 드러난다.
여기서 끝이 아니다. 앞서 언급한대로 내연기관 자동차에 하이브리드 구동계를 추가하면 무게가 크게 늘어난다. 단적인 예로 7세대 쏘나타 하이브리드 버전은 2.0ℓ 가솔린 버전보다 125kg 무거웠다. 하지만 이번에 출시한 신형 쏘나타 하이브리드는 전동화 시스템 구조를 혁신해 LF 쏘나타 하이브리드 대비 무게를 90kg 줄였고 연비는 더욱 높였다.
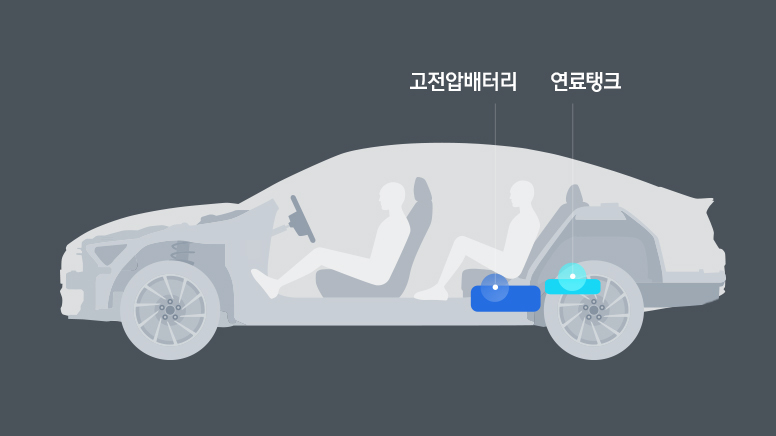
신형 쏘나타 하이브리드는 배터리 출력 밀도를 높이면서 크기를 소형화 했다. 구체적으로 출력 밀도를 21% 높이면서 부피는 16%(7.1ℓ) 줄여, 배터리 시스템의 무게가 16kg이나 가벼워졌다. 더 가볍고 작아진 배터리를 뒷좌석 아래로 배치해 차체 중앙에 낮게 위치시켜 주행성능도 향상시켰다. 또한 하이브리드 제어기(HPCU)를 신규 개발해 부피는 9.5%(7.6ℓ), 무게는 9kg 줄였다.
경량 소재 적용 및 엔진 다운사이징
경량화 기술에는 경량 소재 적용 및 엔진 다운사이징도 빼놓을 수 없다. 경량화 소재의 대표 부품은 알루미늄이다. 차기 제네시스의 모델은 기존 경량화 기술과 함께 알루미늄 적용을 대폭 확대해 더욱 가볍게 만들 예정이다.
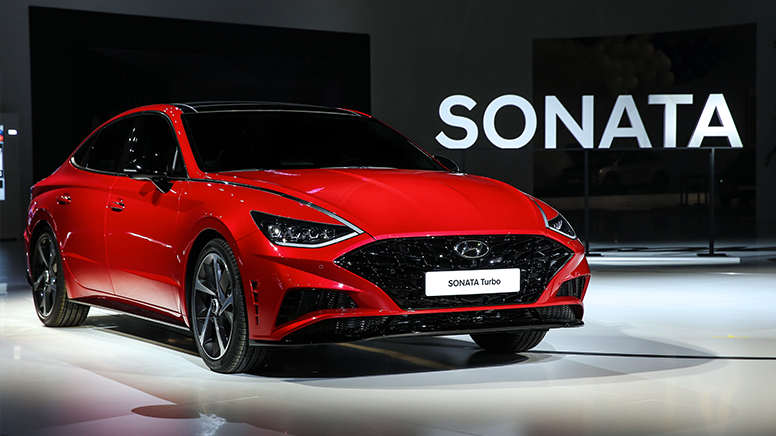
터보 기술을 활용해 배기량을 줄이면서도 출력과 토크를 높이는 파워트레인 다운사이징 기술도 경량화 기술의 중요한 요소다. 하반기 출시예정인 신형 쏘나타 터보는 스마트스트림 G1.6 T-Gdi 엔진을 탑재 예정인데, 경량화를 달성하면서도 월등한 성능을 발휘할 것으로 기대된다.
경량화를 위한 현대·기아차의 숨은 기술
경량화를 위한 현대·기아차의 기술은 작은 부분에도 숨어 있다. 재료기술(재료개발센터)과 생산기술(생기개발센터)의 협업으로 개발하고 양산 적용한 초저비중 실러(초경량 접착제)가 그 예다. 실러란 차체 판넬이 겹쳐지는 부분의 수밀과 방청 역할을 맡는 접착체다. 일반적으로 차 한 대당 6~8kg 정도가 쓰이고 길이를 쭉 늘여 놓으면 150~170m에 달할 정도로 길다.
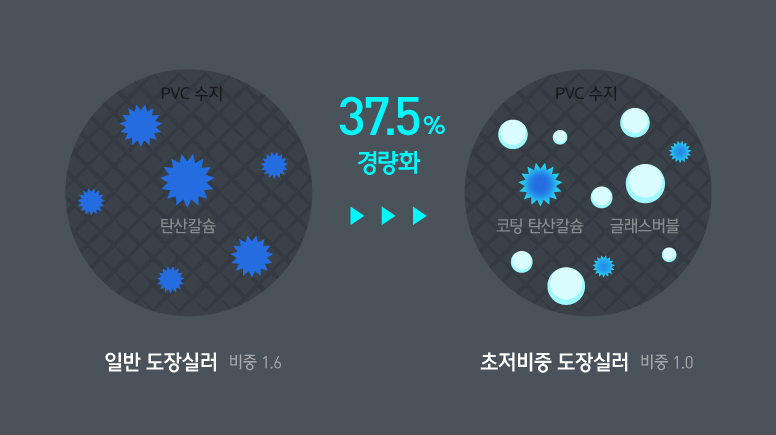
초저비중 실러의 핵심은 기존 실러의 충진재(함량 50%)를 비중 2.9인 탄산칼슘에서 비중 0.38인 초경량 신소재 글래스버블로 대체하는 데 있다. 주성분이 돌가루인 탄산칼슘 대비 글래스버블은 외벽은 유리층이고 내부는 진공으로 된 중공체 초경량 신소재로서, 항공기와 건축 등의 분야에서 고급 단열 충진재로 사용 중이다.
글래스버블의 적용으로 실러 본연의 기능은 그대로 유지하면서 기존 대비 무게를 37%나 줄일 수 있어 약 3kg의 무게 절감이 가능하다. 이 기술은 현대·기아차의 다양한 차종에 확대 적용 중이다.
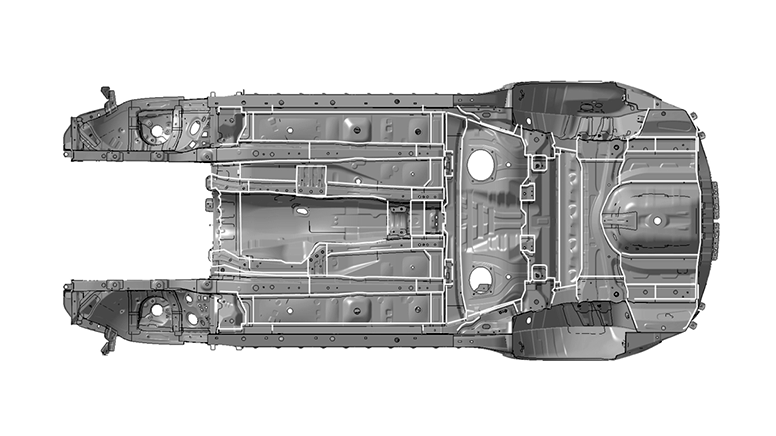
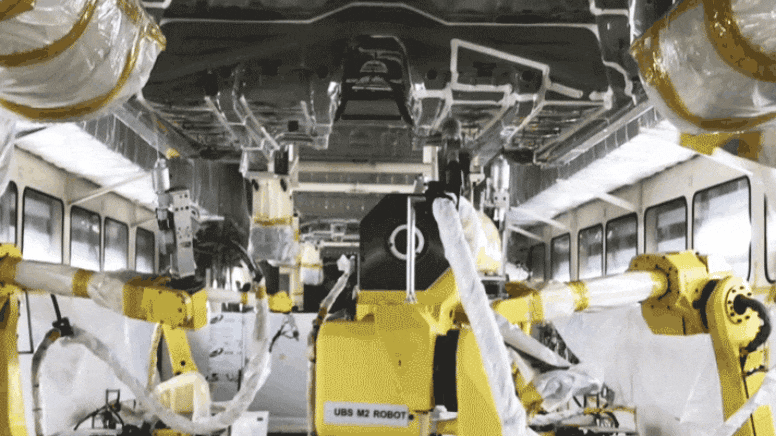
‘고작 2~3kg의 무게가 경량화에 무슨 도움이 되겠냐’고 생각할 수도 있지만 경량화는 어떤 한 부품에서 수십kg의 극적인 무게 감량으로 이뤄지는 게 아니다. 부품 하나 하나의 기술이 차곡차곡 쌓여 전체적인 무게 감량으로 이어지는 것이다.
현대·기아차의 경량화 로드맵
초저비중 실러는 현대·기아차의 경량화 기술 중 극히 일부분에 불과하다. 현대·기아차는 신규 파워트레인 및 플랫폼 적용 등을 통해 향후 출시되는 신차의 중량을 기존 대비 최대 5% 줄이는 것을 목표로 하고 있다. 이를 위해 연구소 차량분석팀 주관으로 중장기적인 차량 경량화 로드맵을 세워 기술을 연구하고, 신소재와 공법을 개발 및 양산 진행 중이다. 차체, 무빙, 내/외장, 플랫폼, 섀시, 전자, 환경기술시스템 등 차량의 전분야에 걸쳐 기술 개발 및 양산을 위한 노력을 기울이고 있는 것이다.
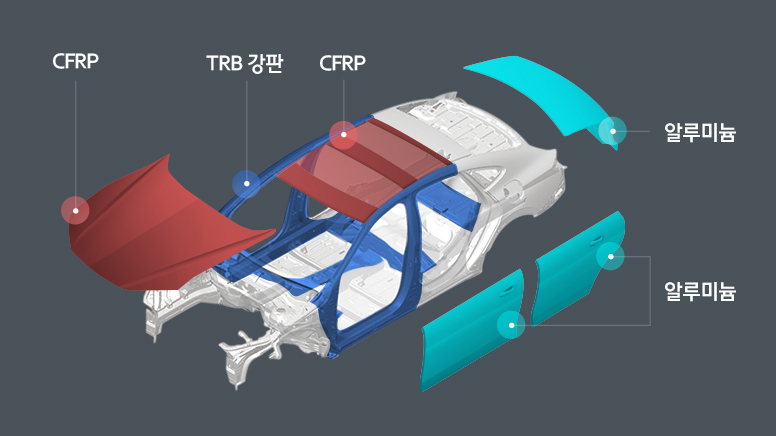
앞서 언급한 CFRP를 포함해, 마그네슘, 티타늄 복합 재료와 같은 최첨단 융복합 신소재의 개발도 진행 중이다. 섀시나 차체 등 강성이 중요한 부품은 주로 초고장력강 등의 금속재료를 개발하고, 내장, 루프, 보닛 등은 고분자 신소재를 개발하는 전략을 병행하고 있다. 또한, 전동화를 대비해 EV용 알루미늄 플랫폼 및 배터리 차체 일체형 구조도 추진 중이다. 전자 분야에서는 부품의 기능을 통합해 하나의 부품이라도 줄임으로써 경량화에 힘을 쏟고 있다.
사람이 다이어트를 통해 단기간에 몸무게를 줄이기 힘든 것처럼 자동차 역시 단기간 내에 무게를 줄이기란 쉽지 않다. 하지만 현대·기아차는 하나의 시스템만이 아닌 전체 시스템의 유기적인 협업으로 적극적으로 경량화를 추진하고 있다. 신형 쏘나타 뿐만 아니라 앞으로 나올 현대·기아차의 신차는 더 가볍고 강하며 민첩해진 모습으로 소비자들을 만족시킬 것으로 기대된다.