카본 자전거는 어떻게 만들어질까? 가볍고 단단한 자전거, 카본 프레임 제작과정!
카본 자전거는 어떻게 만들어질까? 가볍고 단단한 자전거, 카본 프레임 제작과정!
카본 자전거는 어떻게 만들어질까?
대략적으로 탄소섬유로 만든다는것만 알고있었고, 정확히는 모르고있었기 때문에 궁금증을 이기지 못하고 조사를 시작했습니다.
먼저 카본 자전거는 탄소섬유(Carbon fiber)라는 재료로 만들어집니다.
탄소섬유(Carbon fiber)란?
탄소 섬유는 직경이 약 5~10마이크로미터 이고 대부분 탄소 원자로 구성된 섬유를 뜻합니다. 강도, 강성, 고온내성, 가벼운 무게와 같은 많은 장점을 가지고 있습니다.
또 탄소 섬유는 한 방향으로 힘을 가할때는 아주 강하지만, 다른방향으로는 잘 휘어지는 성질을 가졌습니다.
이런 성질을 때문에 단방향 탄소섬유를 격자로 쌓아서 자전거에 사용하기도 합니다.
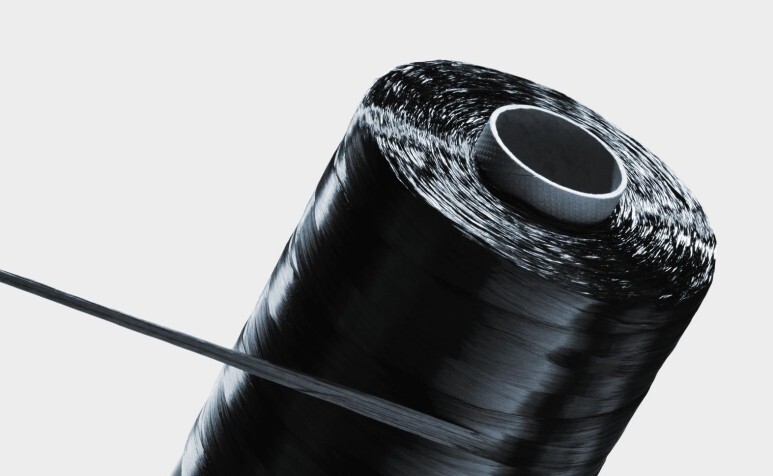
출처 craftechind.com
탄소섬유를 어떻게 층층히 쌓느냐에 따라서 탄소시트의 성질이 달라지기 때문에, 탄소섬유자체보다 탄소섬유를 쌓는 방식과 기술이 더 중요합니다. 자전거회사들은 탄소섬유 쌓는 자기만의 방식을 통해 독자적인 자전거를 만듭니다.
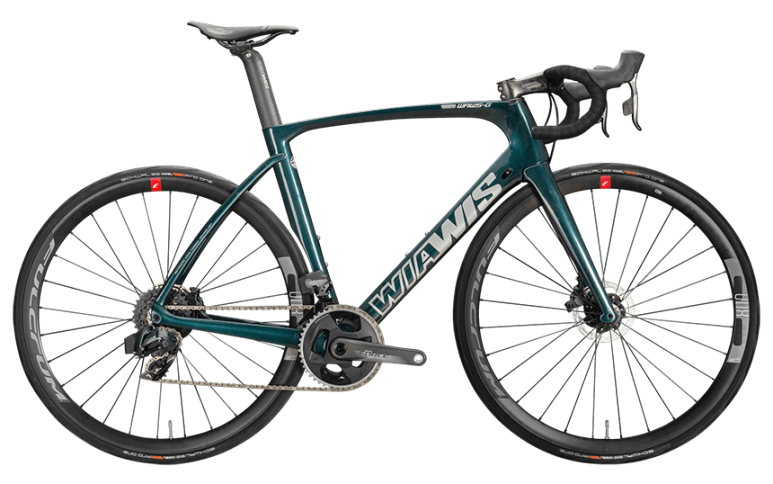
출처 wiawis.com
카본자전거 아주 복잡하고 많은 단계로 만들어집니다.
카본프레임 하나를 만드는데 400개의 카본시트 조각으로 만들어진다고 하네요.
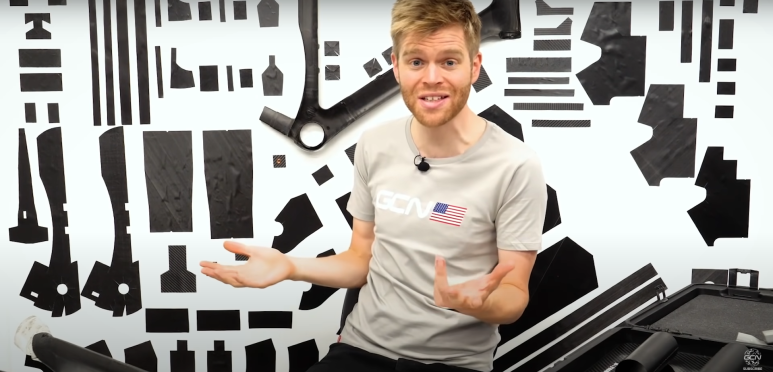
아, 그리고 이번 포스팅을 만들면서 GCN(Global Cycling Network) 유튜브 : LOOK사 사이클공장 견학을 주로 참고했습니다.
※출처/링크는 포스팅 하단에 모아뒀습니다.
자전거 브랜드마다 카본프레임 제작 방식은 다르겠지만, 저는 오늘 LOOK사의 방식을 대략적으로 소개해드리려고 합니다.
SETP 1 : MAKING CARBON FIBER
제일먼저, 탄소섬유를 에폭시 수지랑 섞어서 PREPREG CARBON을 만듭니다.
이 PREPREG CARBON을 롤로 쭉쭉 뽑아냅니다.
탄소섬유 + 에폭시 수지 = PREPREG CARBON!!
이놈으로 자전거를 만듭니다.
PREPREG 란?
프리프레그(Prepreg)는 탄소섬유나 유리섬유와 같은 섬유 강화재에 에폭시 수지와 같은 액상 합성수지를 침투시킨 복합재 중간단계 소재로 최종 부품형틀에서 열과 압력을 받으면 기계적, 열적 물성이 뛰어난 복합재 부품(composite part)이 만들어진다.
[네이버 지식백과] 프리프레그 [Prepreg] (매일경제, 매경닷컴)
각각의 탄소 섬유가닥을 어떻게 배치하느냐에 따라 탄소섬유의 종류가 달라집니다.
탄소섬유는 격자모양으로 짤수도 있고, 단방향으로 짤 수도 있습니다.
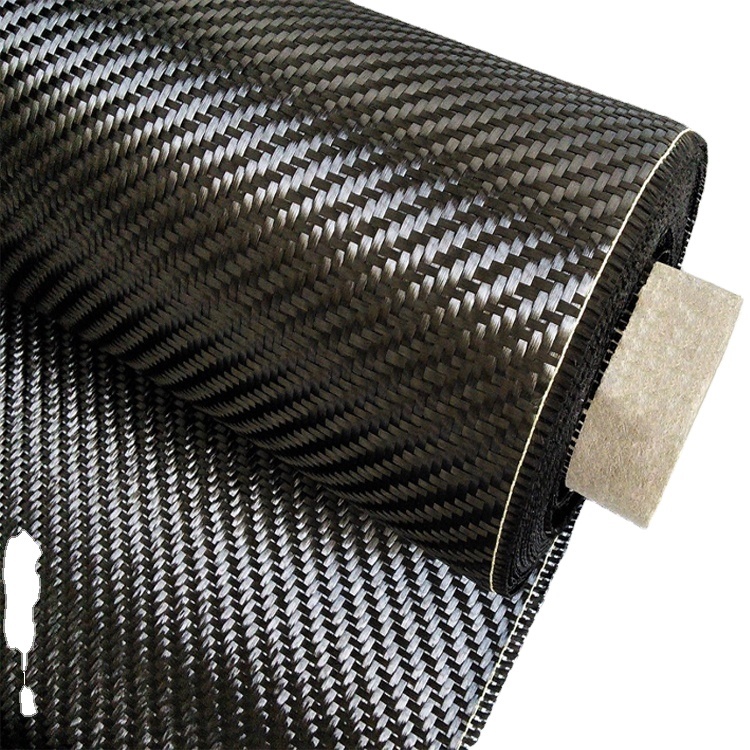
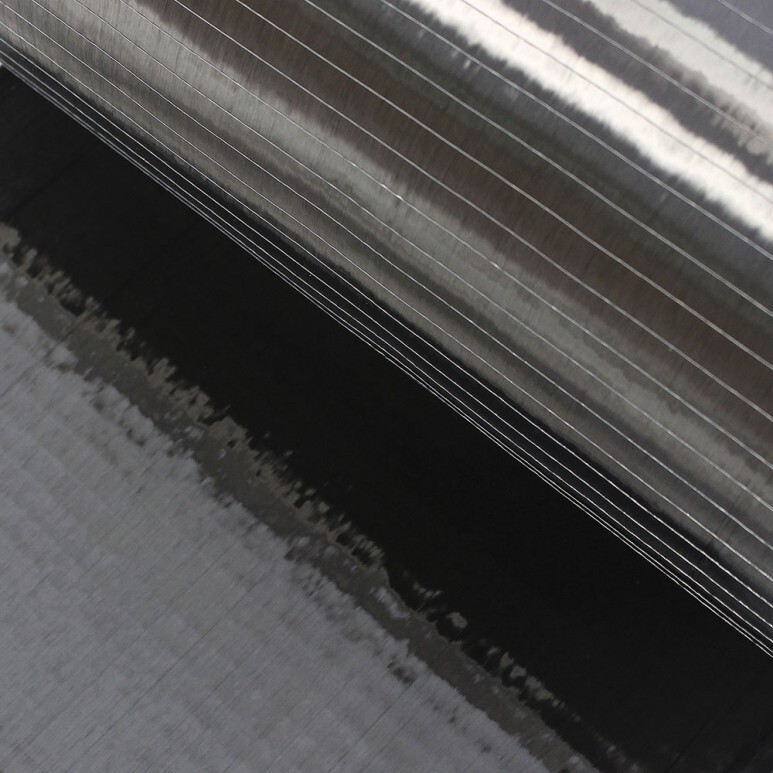
wooven fiber(출처 : alibaba.com)/ uniderctional fiber (출처 : fibreglast.com)
어떻게 탄소가닥을 배치하느냐에 따라 특성이 달라지기때문에, 사용목적에 따라 적합한 탄소섬유를 조합해서 사용하는게 중요합니다.(ex 단단하다고 다 좋은건 아님)
SETP 2 : CUTTING OUT THE CARBON FIBRE
커다란 롤에서 나온 탄소섬유를 커다란 직사각형 모양으로 자르고,
이 친구들을 다시 CNC나 손을 이용해 조각내서 자라줍니다.
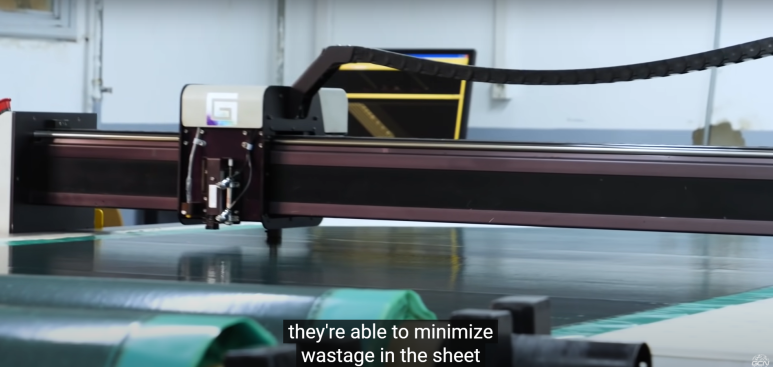

SETP 3 : ASSEMBLING
이제 준비된 탄소섬유를 붙여 프레임을 만들 차례에요.
UNIDIRECTION FIBER을 격자방향으로 번갈아 층층히 쌓아서 제작합니다.
이렇게 하면 각각의 방향에서 스트레스를 견딜 수 있게 제작 가능하다고 합니다.
진행자가 들고있는 하얀 틀(Pre-former)에 카본시트를 정성스럽게 붙입니다.
수작업이었다니, 카본자전거가 비싼 이유가 있었네요...
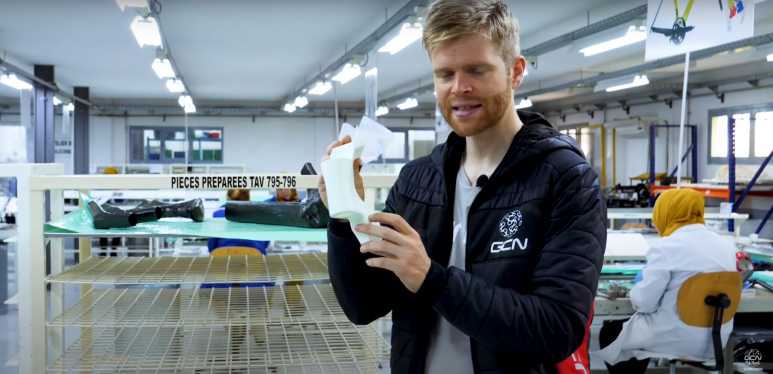
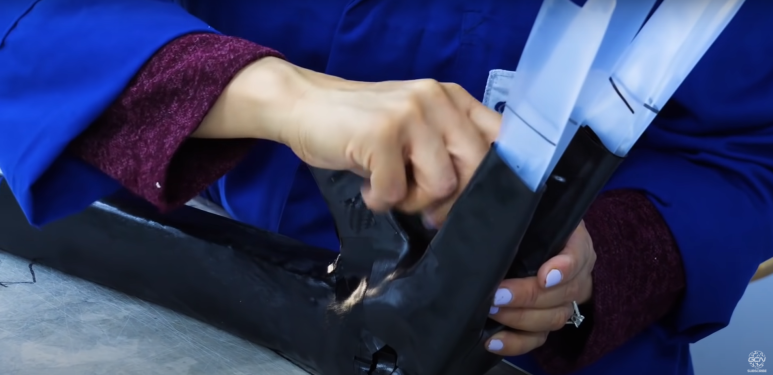
우리 주변에서도 이런 사례를 찾아볼 수 있는데요, 국내 프리미엄 자전거브랜드인 위아위스는 탄소 시트를 자사만의 기술을 활용해 배열하는 특허를 가지고 있습니다. 위아위스는 요즘 올림픽 양궁 활 제작사로 유명하기도하죠
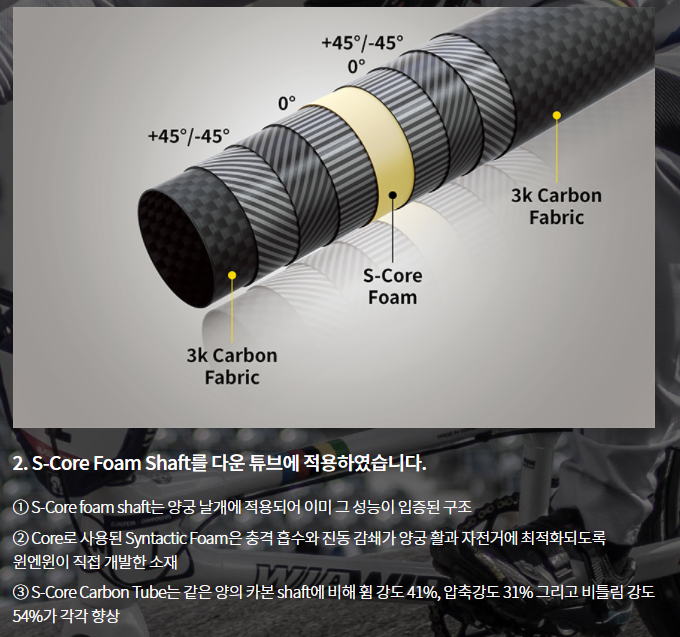
위아위스 S-CORE FOAM SHAFT
TMI) 위아위스는 카본 말고도 S-CORE Foam이라는 코어를 사용해 휨강도/압축강도를 높였다고 하네요.
(S-CORE Foam : 기포강화 플라스틱이다. 수지, 경화제, 필러 및 소포제를 이용하여 배합될 수 있다.)
SETP 4 : MOULDING
다음은 몰딩작업입니다.
밑 사진처럼 미리 만들어진 개별의 파트들을 (시트튜브, 포크 등등)
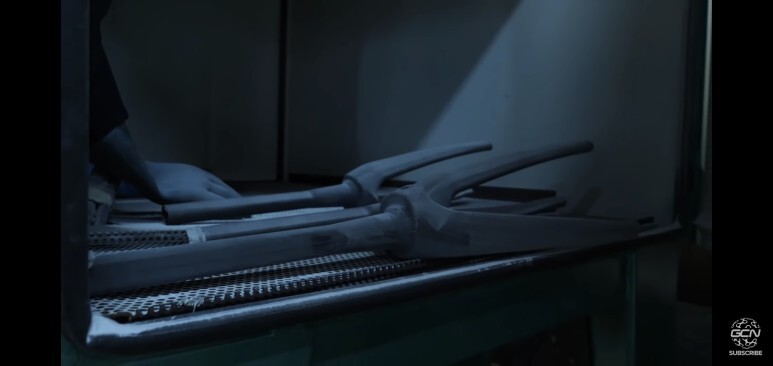
까만 똥같이 보이는 전용 접착제로 붙인 후
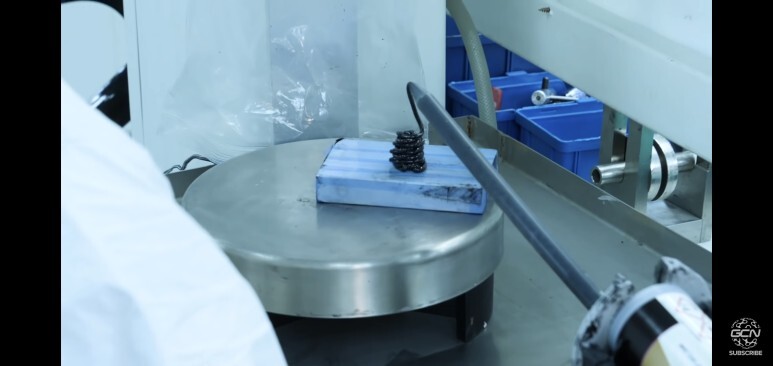
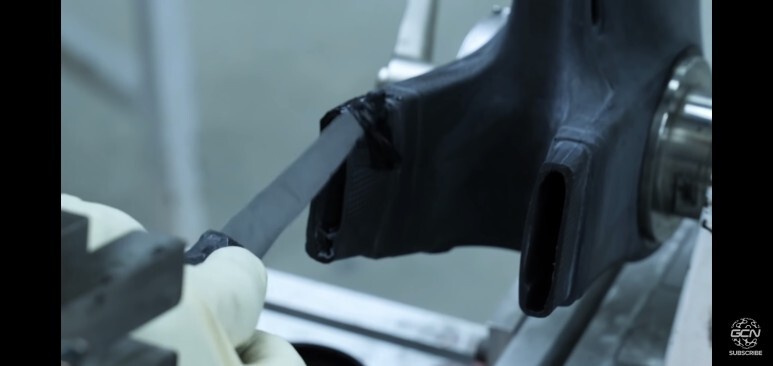
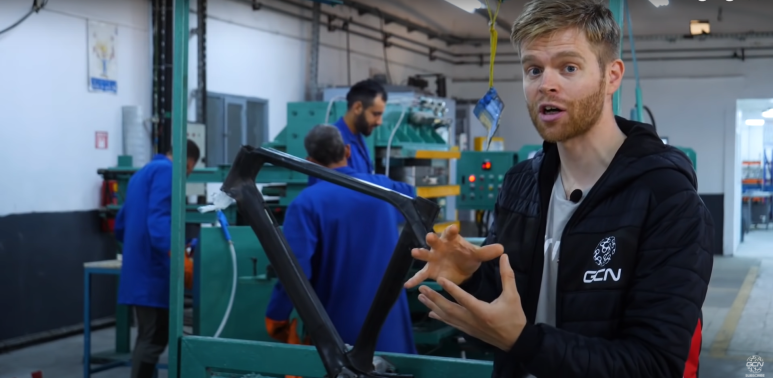
밑에 보이는 거대한 프레스의 틀에 넣고 170도의 온도에서 압력을 2 ->10 bar로 점진적으로 증가시킵니다.
45분동안 작업한다고 합니다.
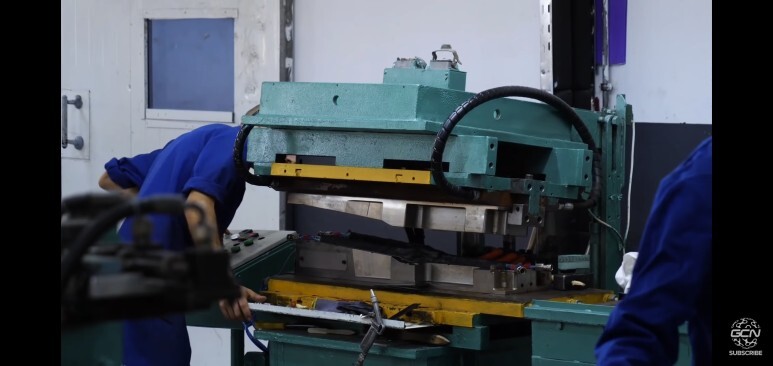
SETP 5 : DEBULKING
카본프레임이 프레스 안에 들어갔을때, 외부에서 압력과 온도가 프레임 방향으로 가해지고, 안에서는 자재가 팽창하면서 카본프레임이 강하게 압축되게 됩니다. 이를 통해 각각의 카본층들의 주름이 펴지게되고, 카본프레임안에 섞여있던 작은 기포들도 빠져나가게 되면서 프레임이 더욱 단단해집니다.
아직까지 처음 카본시트를 붙였던 틀(Pre-former)이 남아있습니다.

몰딩작업 후 밖에서 50분정도 식히며 열이 나가길 기다립니다.
그리고 표면이나 가장자리에 남아있는 잔여물,조각들을 제거합니다.
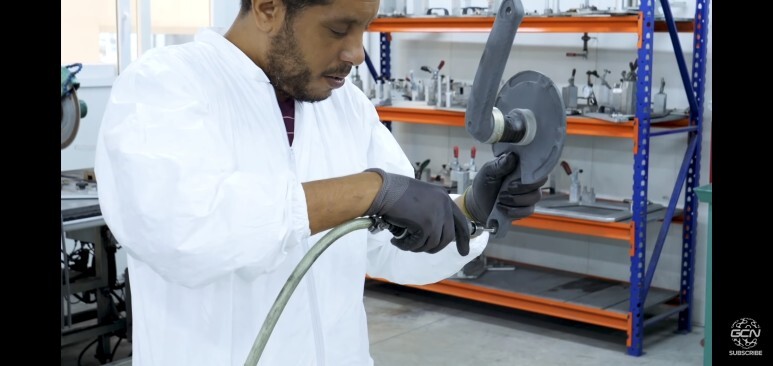
SETP 6 : CURING THE RESIN
이제 카본 프레임을 뒤에 보이는 거대한 오븐에서 굽는 일이 남았습니다. 프레임을 더 단단하게 만들어주고, 프레스 안에서 미쳐 빠져나가지 못한 수분이나 기포를 밖으로 빼주는 과정입니다.
가마에서 도자기를 굽는 과정과 비슷하다고 생각하시면 됩니다
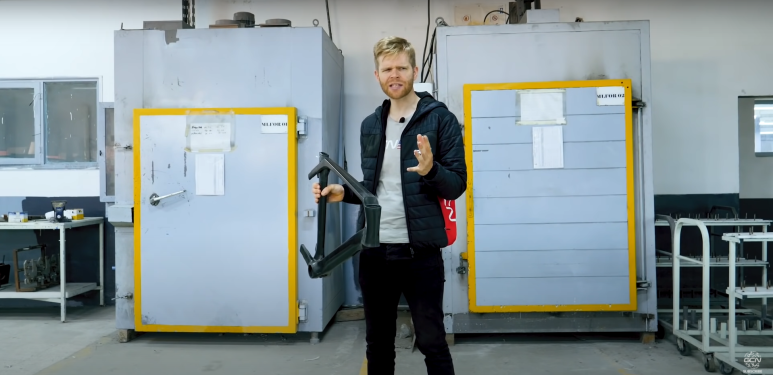
SETP 7 : SURFACE PREPARATION
오븐에서 열처리까지 마쳤으니 표면처리를 해야합니다.
이 아저씨가 들고있는 오른쪽에 있는게 막 베이킹이 끝난 프레임이고, 왼쪽에 회색빛을 띄는게 표면처리가 끝난 프레임입니다.
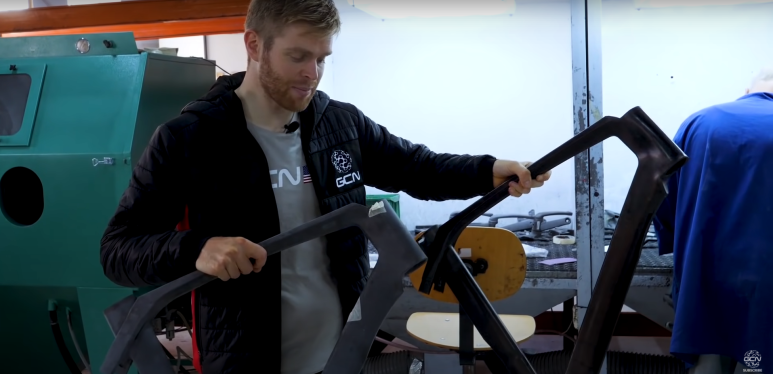
그리고 표면 처리 전에, 카본프레임 안에 있는 조형틀(Pre-former)를 제거해줍니다.
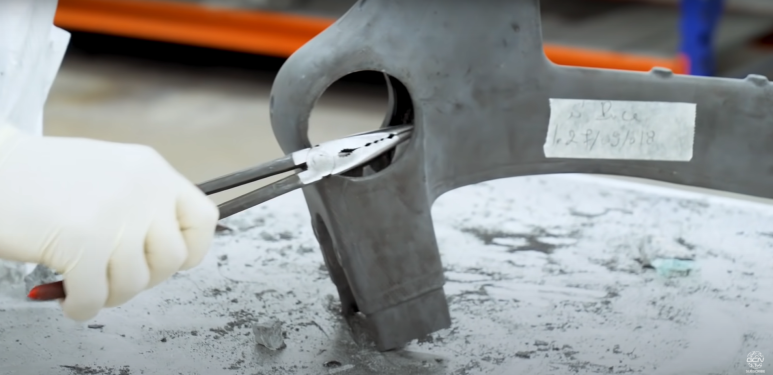
SETP 8 : MACHINING
표면처리가 끝난 프레임조각들은 MACHINING이라는 과정을 거칩니다. LOOK사는 로봇 암을 사용해 정밀작업을 합니다. 행거나 케이블 홀에 필요한 구멍을 뚫고, 필요없는 부분을 디테일하게 절단하는 과정을 거칩니다.
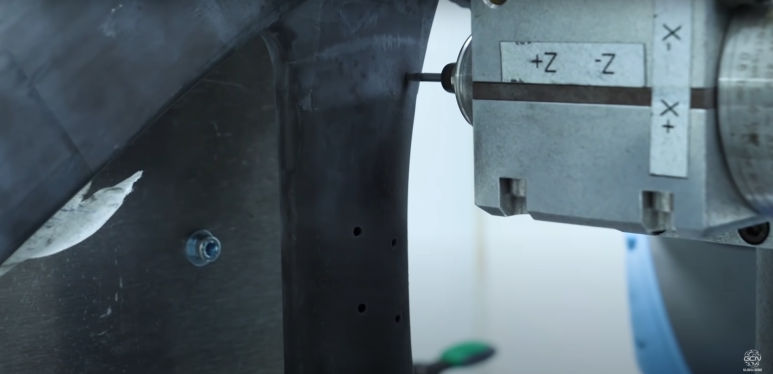
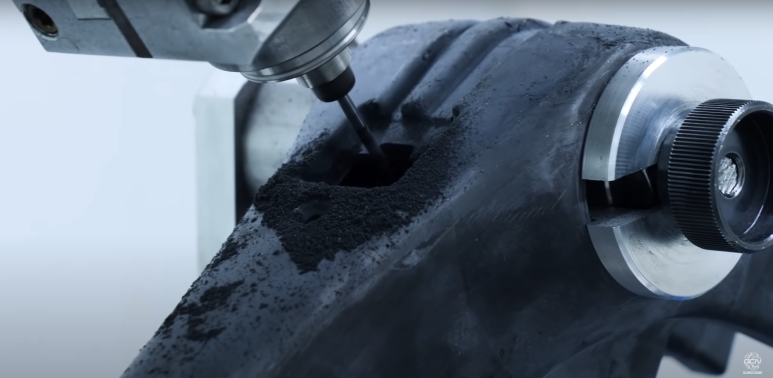
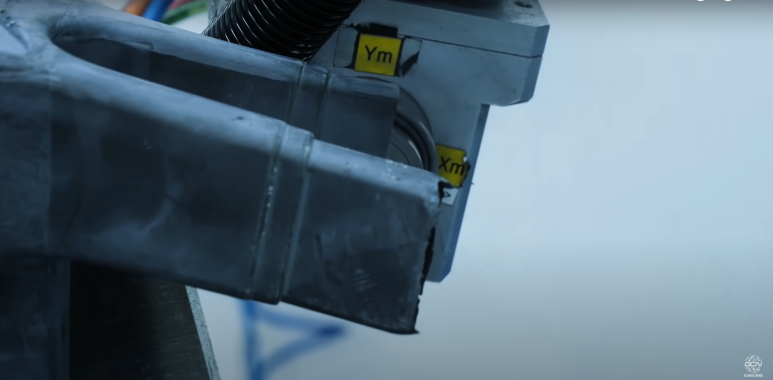
SETP 9 : JOINING THE FRONT AND REAR TRIANGLE
이제 프레임 부품들을 서로 이어붙이는 작업이 남아 있습니다.
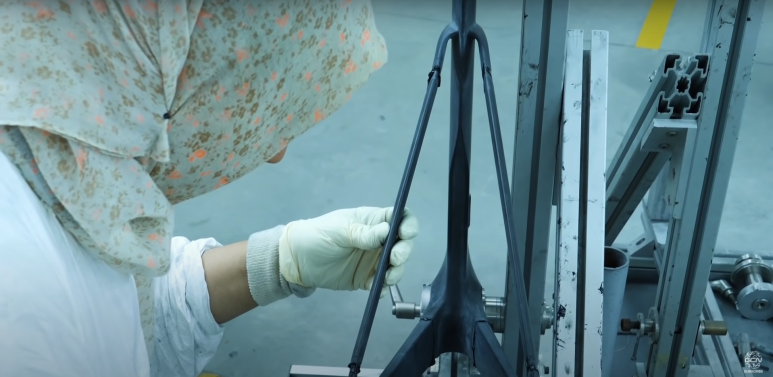
진행자가 가리키는 곳이 카본프레임이 접합되는 부분입니다.
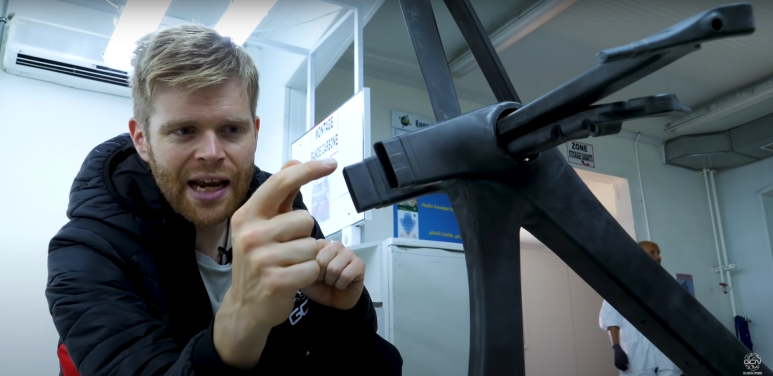
이렇게 맞닿는 부분이 약간 직경을 작게만들어, 이어붙였을때 매끈한 표면이 나오고 단차를 줄일 수 있게 합니다.
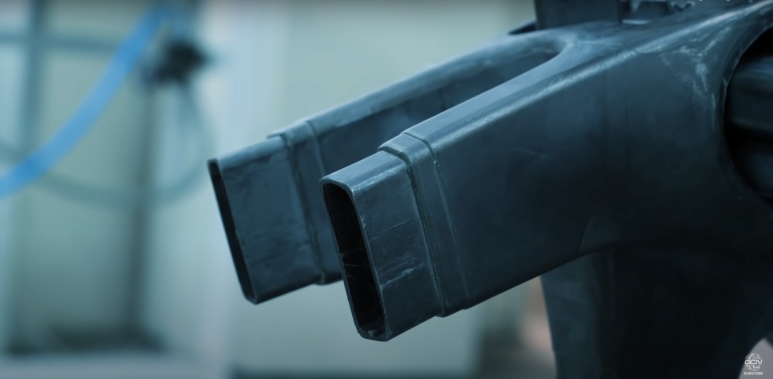
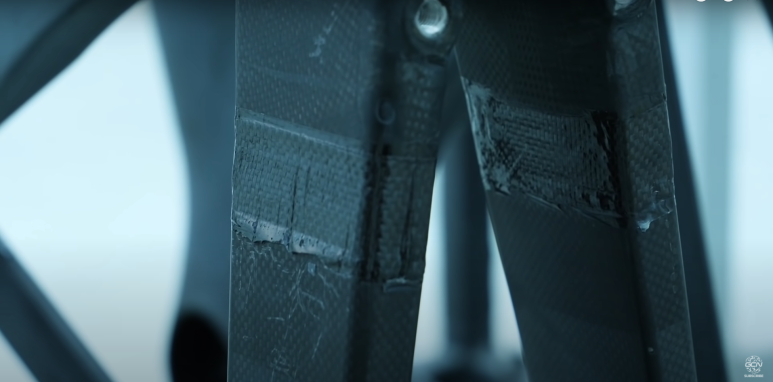
서로 다른 두 카본프레임을 접합할 때는 밑에 보이는 특수 탄소섬유 접착제를 사용합니다.
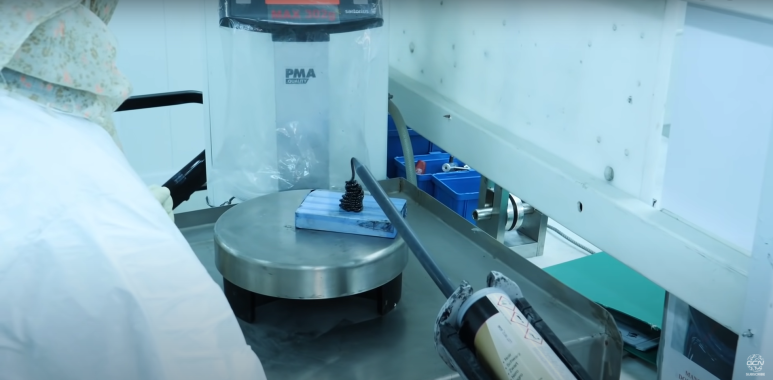
특수 접착제를 사용해 붙이는 과정에서 맞춤 제작된 지그를 사용해 오차없이 제작되도록 해줍니다.
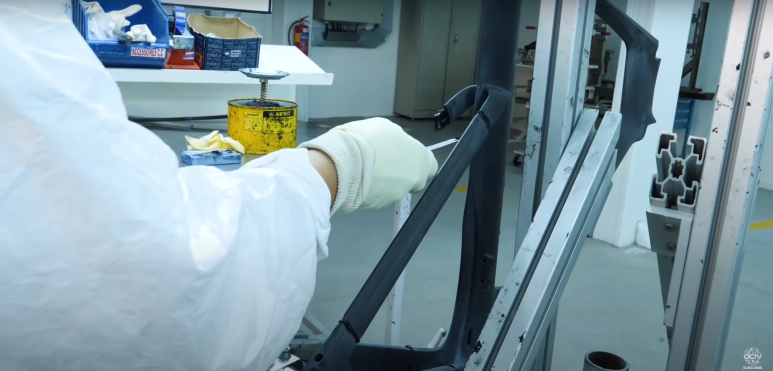
그리고 90도의 온도에서 1시간동안 다시 경화과정(CURING)을 거칩니다.
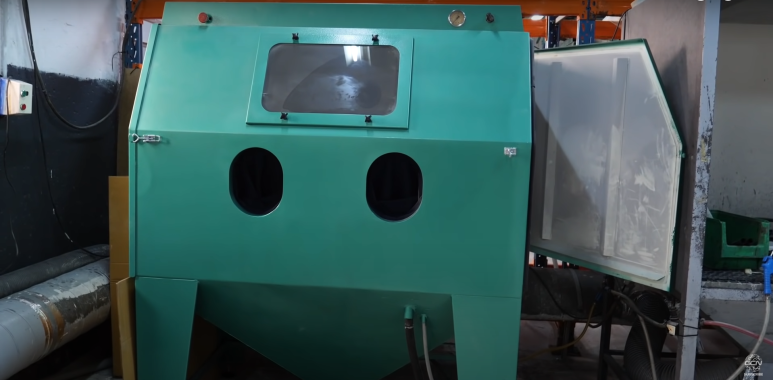
SETP 10 : SURFACE FINISHING
이제 거의 막바지입니다. 조립된 프레임과 각각의 부품들은 마지막 표면처리 작업을 해줍니다.
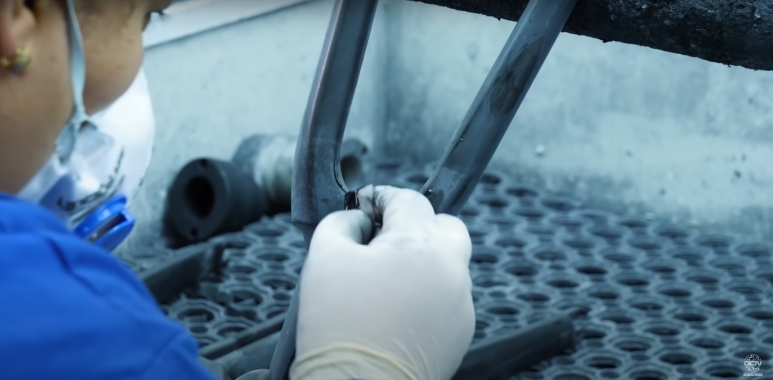
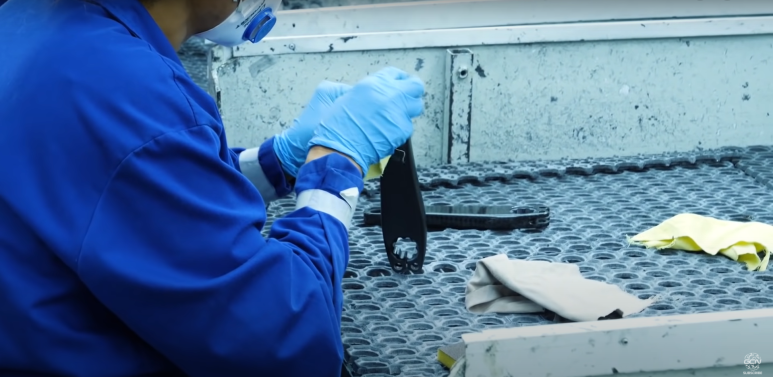
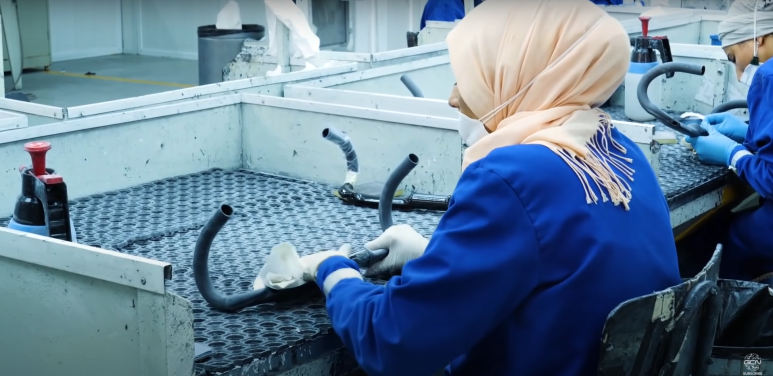
이 과정에서 불량품을 재활용하거나, 폐기처분할 수 있도록 선별해줍니다.
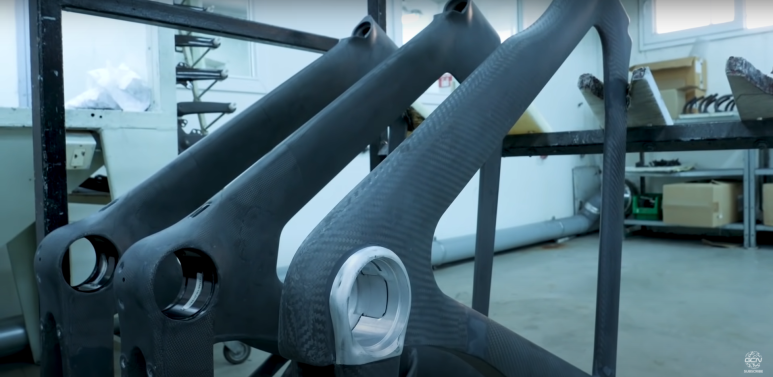
또 밑 사진처럼 표면처리 되지 않은 프레임을 세척하고 샌딩합니다.
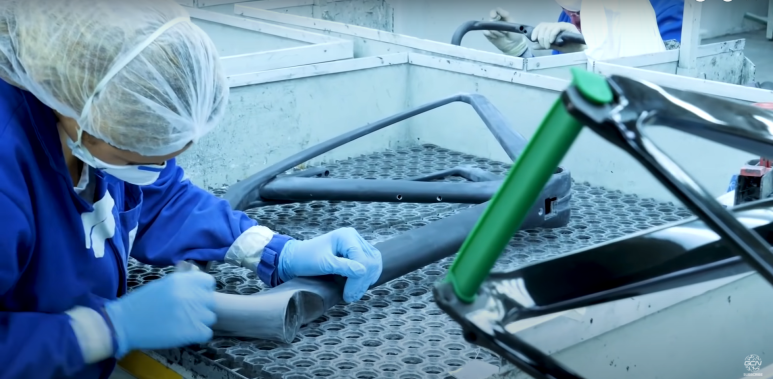
마지막으로 광택이 나도록 작업해줍니다. 이제 페인팅 작업만 남았습니다.
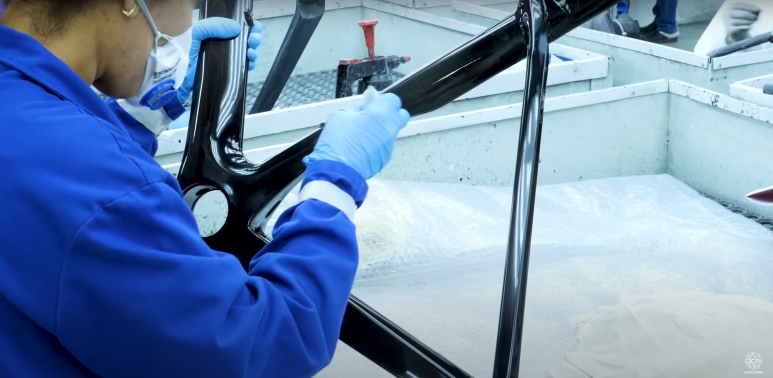
SETP 11 : PAINTING & DECAL
마지막 작업인 페인팅, 스티커 작업입니다.
LOOK사의 경우 튀니지 공장에서 프레임을 제작한 후, 프랑스 본사에서 페인팅작업을 한다고 하네요.
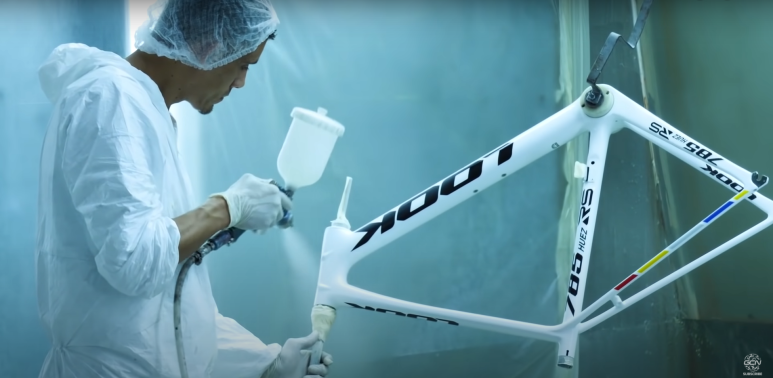
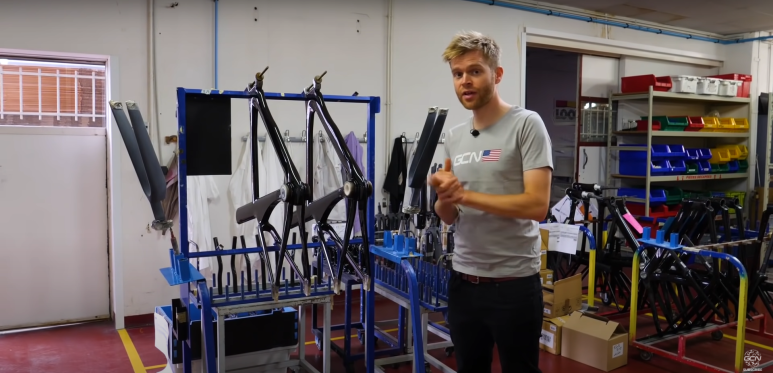
마지막 으로 스티커를 붙여주고 끝이납니다 ㅎㅎ
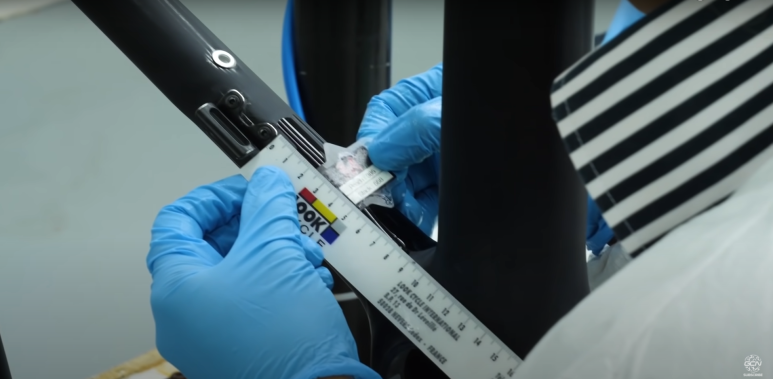
정말 길고 복잡한 과정을 통해, 카본프레임이 드디어 완성되었습니다.
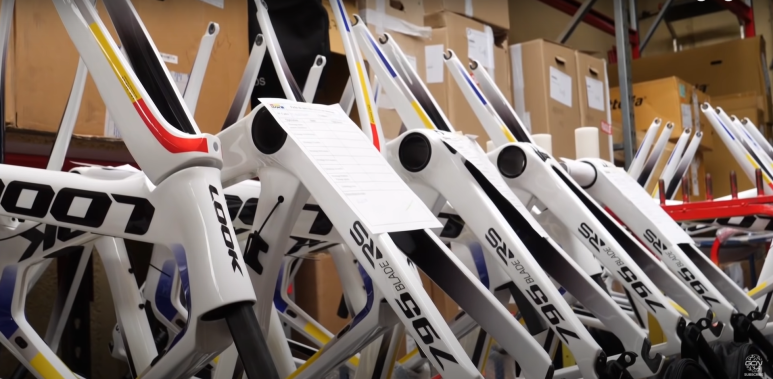
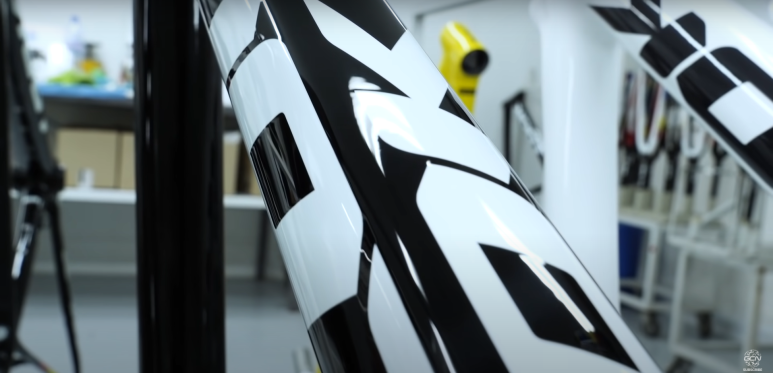
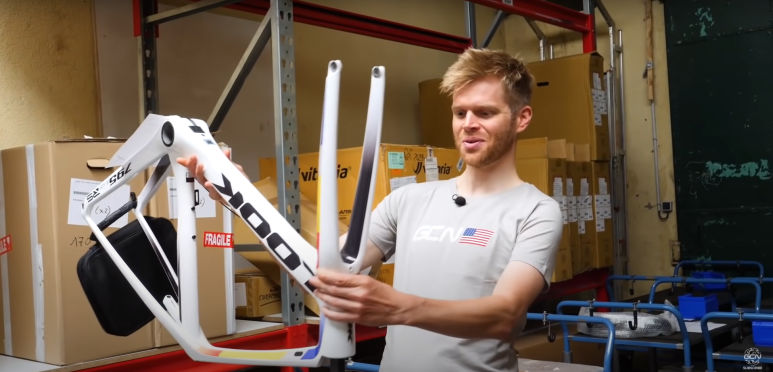
이번 포스팅을 작성하면서, 정말 카본프레임 자전거가 왜이렇게 터무니없이 비싼지 조금 알게된 것 같습니다. 정말 많은 기술과 노력이 들어가네요. 그래도 아무 불평없이 사기에는 아주 비싼 금액이긴 합니다. 각 브랜드별로 기함급은 1000만원이 넘어가니...
하지만 화학공학과 학부졸업생으로서 흥미로운 조사였다고 생각합니다. 수원 자린이 여행하는 노이였습니다. 진성 자덕이 되는날까지 정진하겠습니다.
다음 포스팅 때 뵈요!